PCBA加工流程中的贴片和焊接要求
在电子制造业中,PCBA(印刷电路板组装)作为电子产品的核心部分,其加工流程中的每一个步骤都至关重要。特别是贴片和焊接环节,它们直接决定了PCBA加工的质量以及最终产品的性能。作为PCBA代加工工厂的资深人员,本文将简述这两个关键步骤中的要求和注意事项。
一、贴片要求
- 元器件准备:
- 元器件必须按照BOM(物料清单)进行严格筛选,确保型号、规格、数量与要求一致。
- 元器件必须经过外观检查,确保无损伤、无污渍、无氧化等缺陷。
- 元器件应存放在干燥、无尘的环境中,避免受潮或污染。
- 贴片机校准:
- 贴片机应定期进行精度校准,确保贴片位置的准确性。
- 根据元器件的大小和形状,选择合适的吸嘴和贴片参数。
- 贴片操作:
- 贴片过程中,应确保PCB板面清洁,无杂物、无油污。
- 贴片速度应适中,避免过快导致元器件飞落或位置偏移。
- 对于细小或特殊的元器件,应采用特殊的贴片方法和工具。
- 贴片后检查:
- 贴片完成后,应进行目检,确保元器件位置正确、无倾斜、无缺失。
- 使用AOI(自动光学检测)设备对贴片结果进行复检,提高检测效率和准确性。
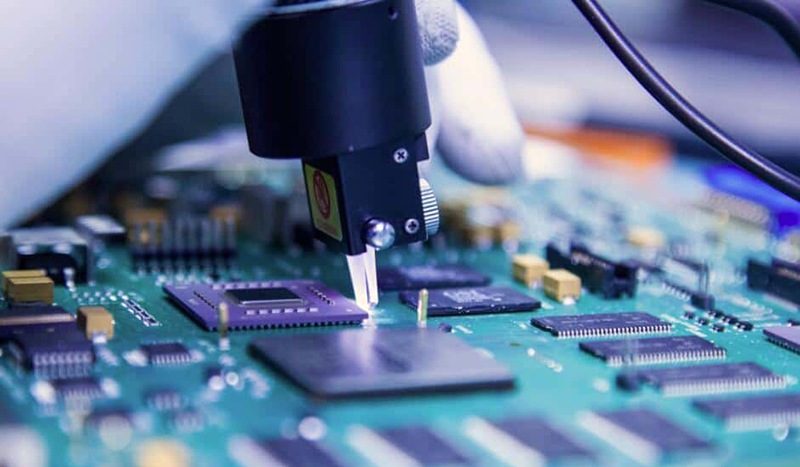
二、焊接要求
- 焊接参数设定:
- 根据元器件和PCB板的材质、厚度,设定合适的焊接温度、时间和压力。
- 避免温度过高或时间过长导致元器件损坏或PCB板变形。
- 焊接环境:
- 焊接区域应保持清洁,无灰尘、无杂物。
- 确保焊接设备接地良好,避免静电对元器件造成损伤。
- 焊接操作:
- 焊接前应对PCB板进行预热,减少焊接过程中的热应力。
- 焊接过程中,应确保焊锡均匀覆盖元器件引脚和PCB板焊盘。
- 避免焊接过程中出现虚焊、冷焊、连焊等不良现象。
- 焊接后检查:
- 焊接完成后,应进行目检和X光检查,确保焊接点饱满、无气孔、无裂纹。
- 使用电性能测试设备对焊接后的PCBA进行功能测试,确保焊接质量符合要求。
三、注意事项
工艺控制:在整个贴片和焊接过程中,应严格控制工艺参数和操作规范,确保产品质量的稳定性和一致性。
人员培训:操作人员应接受专业培训,熟悉贴片和焊接设备的操作方法和维护要求。同时,应提高操作人员的安全意识和质量意识。
设备维护:定期对贴片机、焊接机等设备进行维护和保养,确保设备的正常运行和精度稳定。
质量追溯:建立完善的质量追溯体系,对贴片和焊接过程中的关键参数和数据进行记录和分析,以便及时发现问题并进行改进。
联网设备的制造离不开高精度的PCBA加工流程,而贴片和焊接作为其中的关键环节,其要求和注意事项应得到足够的重视。通过不断优化工艺、提高操作水平、加强设备维护和质量追溯等措施,我们可以确保PCBA的加工质量达到最佳状态,为联网设备的制造提供有力保障。